丰田:骨子里的TPS
当你漫步日本任何一家书店,都会看到满满一书架关于丰田的书籍,这些书藉中,除了极少数是写汽车方面的内容,多数都在写丰田的精益管理理论及实践;而在中国,京东商城上有关精益管理的书籍,少说也有上百种。
如今,在生产型企业,如果你不了解些精益管理的内容,恐怕都难以胜任工作。也许丰田人自己都没想到,没有什么高深理论,只是刻在丰田人骨子里的DNA——TPS(丰田生产方式),1990年被美国麻省理工学院的数位专家研究总结为精益管理或精益生产后,引发全世界各国各行业纷纷拿来学习实践。
有人总结,TPS的核心就是通过杜绝浪费、加速流程、持续改善来为企业创造价值,这三句话说起来容易,但实践起来要复杂得多,它们为何会成为丰田人骨子里的DNA?其他企业可否复制丰田的DNA呢?
持续改善的案例
余明(化名)是丰田(中国)的一名管理人员,日常的工作是在办公室处理相关文职业务,工作跟生产线几乎没有交集。不久前,他参加了公司的一个培训项目,到天津一家丰田的零部件工厂进行为期2周的调研。
这家工厂生产左右转向灯连杆,一条流水线有5 个人,余明的工作就是拿着秒表,记录一位工人完成自己那道工序所用的时间,要精确到0.1秒,同时观察生产过程中是否有浪费。
据悉,以前这道工序做完需要约30秒的时间,余明把工作记录交给相关部门,接下来就是进行改进的过程。比如他观察发现,工人在取物时需要抬手取物,耗时不说,工人比原地取物更累,于是生产线就调整取零部件的高矮位置,以更方便员工取物。
经过一系列的改进,余明观察的那道工序完成时间从过去的30秒缩短了将近4秒,一天下来,时间就节省了很多,工人单位时间内便可以完成更多的成品,减少了加班,降低了成本,这就是丰田精益生产的一个小例子。
学习丰田的价值
如今很多行业都在学习丰田的精益管理。那么把丰田的DNA注入其他行业会发生哪些变化呢?
丰田(中国)相关负责人向《商学院》记者分享了这样一则案例:2011年,日本发生大地震,东北地区满目疮痍,一家水产加工公司希望利用TPS改进生产,重建家园。这一任务交到了丰田公司的"改善能手"友山行政研究员手中。
改善前,员工并不清楚自己的业务内容;改善后,水产公司以周为单位事先安排好每个人的工作,在工厂入口处的白板上明确公示出各自的业务内容。“可视化”的业务安排不仅让每位员工对自身的工作内容了解得清清楚楚,更是一目了然地显示出每个人的工作量。
另外,他们还为每项工作制定了基准时间,实行标准化管理,这样加工过程中的"半成品"就不会被拖到隔天处理。产品质量参差不齐、原材料反复进出冷库等无用工也被减少了。
再比如,改善前全员聚集在一处工作,改善后按工位划分,实施流水线分工作业,这一举措极大地提升了生产量,减少了搬运产生的无用功。不同工位按照事先制定的品质标准实施检查,减少了不良产品的出现。这家只有51名员工的小公司,现在每天最多可以加工3吨食品。同时,鱿鱼加工的生产效率相比TPS改善前提高了约30%。
事实上,中国很多生产型企业也都纷纷学习丰田精益管理模式,通过减少浪费提升效率。
0库存的考验
杜绝浪费是丰田精益管理的核心理念之一。在产品生产过程中,丰田一直追求低库存甚至是0库存,在丰田看来,库存就是浪费,因为过早购买原材料、零部件,占用资金不说,放置零部件需要仓库、运输物流,这些都需要成本。
不过,在新冠肺炎疫情(以下称“疫情”)之下,0库存理念也考验着丰田和诸多学习丰田精益管理的企业。近年来,全球缺芯的话题一直困扰着汽车业,因为缺芯,汽车交付周期变长。之前消费者购买丰田汽车时将收到两把遥控钥匙,不过现在全球缺芯背景下,因库存不足,丰田不得不先给用户交付一把遥控钥匙,过一段时间再交付另一把。
这只是在疫情之下给0库存带来的挑战之一。“我觉得丰田精益管理,包括0库存概念,以及供应商管理、战略管理等概念,这些是非常有意义和有价值的,只是最近一段时间因为受疫情影响,光有0库存还不行,必须有一些预防性措施,大家在为这一制度进行检讨。”奥纬咨询董事合伙人张君毅对《商学院》记者说,尽管管理有一定的国家差异性,但也有其自身的规律,丰田的精益管理,是美国麻省理工学院参观丰田之后总结出来的经验,具有相当的普适效应。当前包括中国企业在内的全球企业中国企业也在认真学习实践丰田精益管理,并在不断充实完善丰田精益管理思想。实现精益化已经成为国际性企业发展的趋势之一。
除《商学院》杂志署名文章外,其他文章为作者独立观点不代表《商学院》杂志立场,未经允许不得转载。版权所有
欢迎关注平台微信公众号
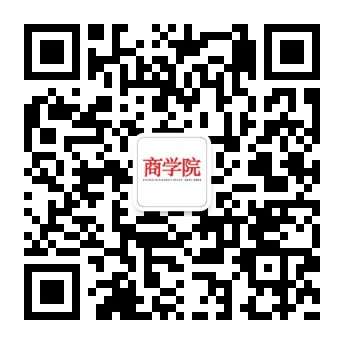